The Evolution of Gabion Manufacturers From Tradition to Innovation
In the realm of construction and civil engineering, gabions have long been a staple for soil erosion control, slope stabilization, and the enhancement of infrastructure. These caged structures, typically filled with rocks or gravel, provide an effective and cost-efficient solution for a wide range of environmental challenges. Over time, the industry has seen significant changes, particularly in the manufacturing process, as companies adapt to evolving market demands and technological advancements.
The history of gabion manufacturing is rooted in traditional craftsmanship, where workers would manually shape and assemble the cages using basic tools and techniques. This method was labor-intensive and time-consuming, limiting the scalability and efficiency of production. However, as the demand for gabions grew, manufacturers began to explore more automated and streamlined production methods.
One of the key turning points in the evolution of gabion manufacturing was the introduction of computer-aided design (CAD) software. This technology allowed engineers to create detailed designs and blueprints, which could then be used to automate the fabrication process. CNC (computer numerical control) machines were also introduced, further increasing the precision and speed of production.
Today, gabion manufacturers are at the forefront of innovation, utilizing cutting-edge technologies such as 3D printing and robotics
Today, gabion manufacturers are at the forefront of innovation, utilizing cutting-edge technologies such as 3D printing and robotics
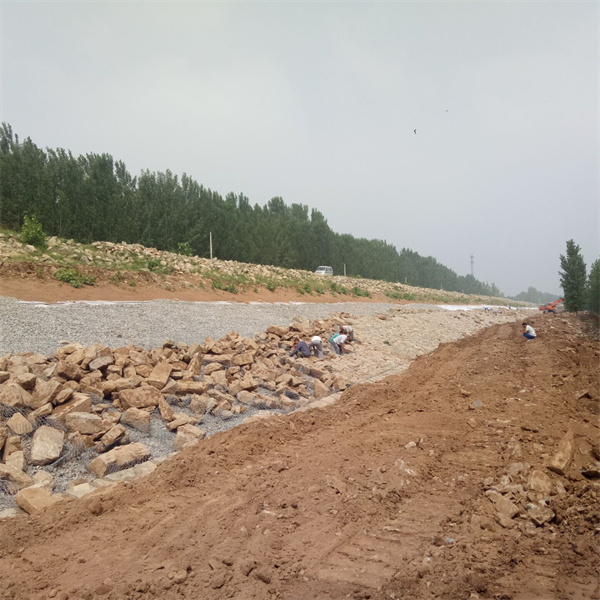
Today, gabion manufacturers are at the forefront of innovation, utilizing cutting-edge technologies such as 3D printing and robotics
Today, gabion manufacturers are at the forefront of innovation, utilizing cutting-edge technologies such as 3D printing and robotics
pronounce gabion manufacturer. These advances have not only increased the speed and efficiency of production but have also expanded the range of materials that can be used in gabion construction. For example, 3D printing allows for the creation of complex geometric shapes and custom designs, while robotics enables the precise placement of materials within the cage.
Moreover, sustainable practices are becoming increasingly important in the gabion manufacturing industry. Many companies are now focusing on reducing their carbon footprint by using recycled materials and implementing energy-efficient production processes. This shift towards sustainability not only benefits the environment but also helps manufacturers stay competitive in a rapidly changing market.
In conclusion, the evolution of gabion manufacturing from traditional craftsmanship to innovative technologies has been driven by the need for efficiency, scalability, and sustainability. As the industry continues to grow and evolve, it is likely that we will see even more advanced and sustainable manufacturing techniques being adopted by gabion manufacturers around the world.