Gabion cages have progressively carved out a niche in construction and landscaping due to their versatility and robustness. When contemplating their use, one primary concern that often arises is their cost. Understanding the intricacies of gabion cage expenses involves examining several factors that pivot around material quality, project scale, design intricacy, geographical location, and installation techniques.
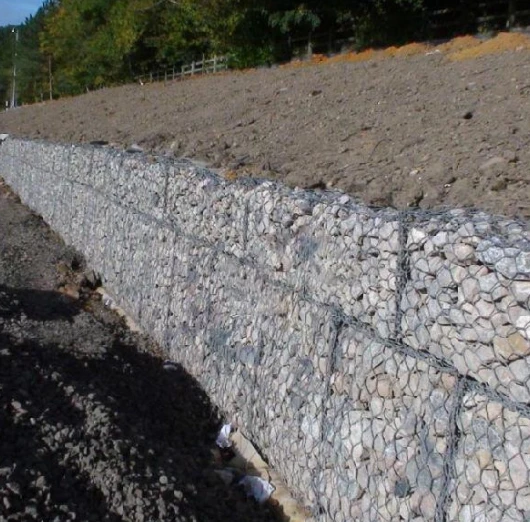
Material choice is pivotal in determining the cost of gabion cages. Typically constructed from galvanized steel, the wire's thickness and coating significantly influence the price. Thicker wires with superior coatings such as Galfan offer enhanced longevity, resistance to corrosion, and increased tensile strength, although they invariably raise the cost. Opting for high-quality materials can be seen as an investment, as they reduce the frequency and cost of future maintenance or replacements.
The project's scale is another determinant of cost. Large projects benefit from economies of scale, where the per-unit cost decreases as the quantity increases. Suppliers may offer discounts for bulk purchases, making extensive projects more cost-effective on a per-cubic-meter basis compared to smaller undertakings. Additionally, considering logistical aspects, ordering gabion cages locally can mitigate transportation expenses, thereby reducing the overall cost.

Design complexity also affects the budget. While standard rectangular gabion boxes are generally economical, custom shapes such as trapezoidal or cylindrical designs might require special fabrication, leading to increased costs. Intricate designs demand more expertise in both manufacturing and assembly, necessitating skilled labor for precision installations.
Geographical factors cannot be ignored when discussing gabion cage costs. The availability of local materials for filling, such as stones and rocks, can substantially impact expenses. In regions where suitable filling materials are scarce or have to be transported over large distances, costs can surge. Conversely, areas rich in natural resources can facilitate cheaper acquisition and subsequently lower installation costs.
gabion cage cost
Installation techniques play a crucial role in determining the final expense. Professional installation ensures that gabion cages are set up correctly, guaranteeing structural integrity and extending their lifespan. However,
professional services come at a cost. For those with DIY capabilities, self-installation can serve as a cost-saving measure. Still, it’s vital to note that improper installation may lead to instability and necessitate costly repairs down the line.
To optimize the gabion cage cost, potential buyers should conduct a thorough cost-benefit analysis. This involves assessing long-term maintenance expenses against initial costs, considering factors such as the environment’s exposure to harsh weather conditions and the specific functional requirements of the gabion structure. For instance, retaining walls in high-moisture areas may need additional treatments or stronger materials, altering the initial budgeting forecasts.
Lastly, complying with local regulations and acquiring necessary permits can also influence the cost. Some jurisdictions impose stringent guidelines on construction materials and techniques, mandating specific standards that might elevate costs. Engaging with a knowledgeable professional who understands these regulatory landscapes can help mitigate unexpected expenses stemming from non-compliance or project delays.
In sum, while gabion cage cost is subject to a myriad of influencing factors, strategic planning and informed decision-making can ensure cost-effectiveness and project success. Investing in quality materials, hiring proficient installers, and understanding local economic contexts can collectively lead to a durable and economically sound gabion cage installation.