Gabion walls have emerged as a versatile option in construction, landscaping, and environmental engineering projects over the years. When considering the materials that ensure the durability and strength of a gabion wall, the quality of the wire is paramount. The wire essentially acts as the backbone, determining the life span and performance of the entire structure.
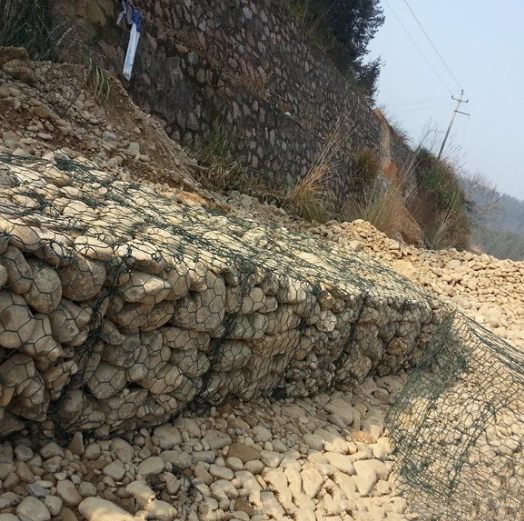
Choosing the right gabion wall wire requires a keen understanding of the factors that influence its effectiveness.
A primary consideration is the wire coating. Zinc-coated and PVC-coated wires are among the most prevalent types used to prevent corrosion. Zinc, being a sacrificial metal, protects the steel from rusting, thereby extending the lifespan of the gabion wall in harsh weather conditions. PVC coating, on the other hand, offers an additional layer of protection, ideal for environments subjected to acidic or alkaline conditions. When I first used PVC-coated wires in a landscape project in a highly saline coastal area, the results affirmed their efficacy; the wires resisted corrosion far better compared to their uncoated counterparts, showcasing the combination of protective layers as a hallmark of quality.
Equally important is the gauge of the gabion wall wire. A thicker gauge wire offers improved tensile strength, which is critical for walls exposed to heavy loads or frequent pressure changes. For base layers in tiered gabion systems, opting for a thicker gauge ensures stability and structural integrity. My experience with a multi-layered retaining wall in a high rainfall area taught me that selecting the appropriate gauge was a decisive factor in preventing bulging or collapses.
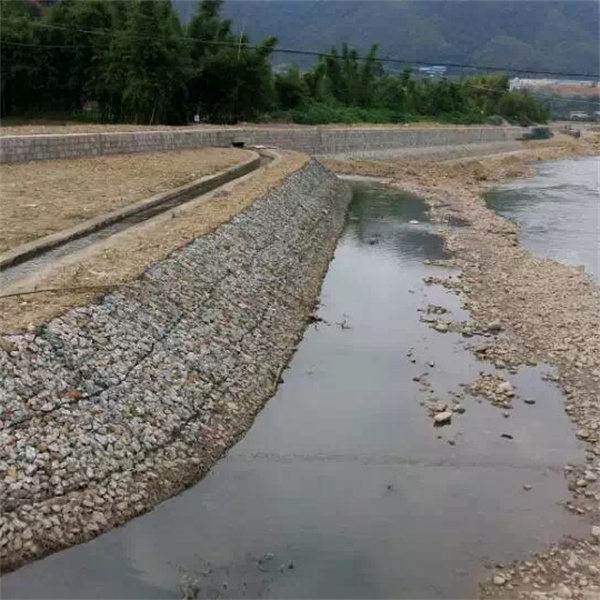
Working in areas with frequent freeze-thaw cycles further highlights the importance of wire selection. In these settings, flexibility is as crucial as strength. Wires that can withstand temperature fluctuations without becoming brittle are essential. I've often recommended the use of high-quality, flexible steel for projects in mountainous regions where frosty conditions prevail. This not only minimizes maintenance concerns but also fortifies the wall against environmental stresses.
gabion wall wire
For those managing projects where a natural aesthetic is desired, such as in garden setups, the wire mesh can be fabricated in a way to support verdant growth on the structure's surface. In one of my earlier projects, selecting a wire mesh with a slightly larger aperture facilitated the growth of vines and climbing plants, blending the structure into its natural surroundings while maintaining its robustness.
Understanding the regulatory standards of gabion wall wires is also key. Compliance with industry standards, such as ASTM or ISO certifications, assures that the wire has undergone rigorous testing. This authoritative endorsement gives confidence in the material's performance over extended periods. In a government infrastructure project I was involved in, adherence to such standards was non-negotiable, ensuring the safety and reliability of the gabion structure over decades.
In conclusion, when selecting gabion wall wire, the emphasis should be on a combination of protective coating, gauge, flexibility, and regulatory compliance. These characteristics guarantee not only the aesthetic and functional success of gabion walls but also their long-term value. Through meticulous planning and informed decision-making, the sturdy yet malleable nature of high-quality gabion wall wire can be harnessed to meet various structural needs, reaffirming its role as a reliable choice in modern construction practices.