Innovative strides in gabion production lines have significantly transformed the construction and landscaping industries, providing robust solutions for a range of infrastructure projects. Gabions, essentially wire cages filled with rocks, have been employed for centuries in riverbank stabilization, retaining walls, and erosion control. The advent of modern production lines has revolutionized the efficiency and precision with which these structures are manufactured, promising greater quality and customization.
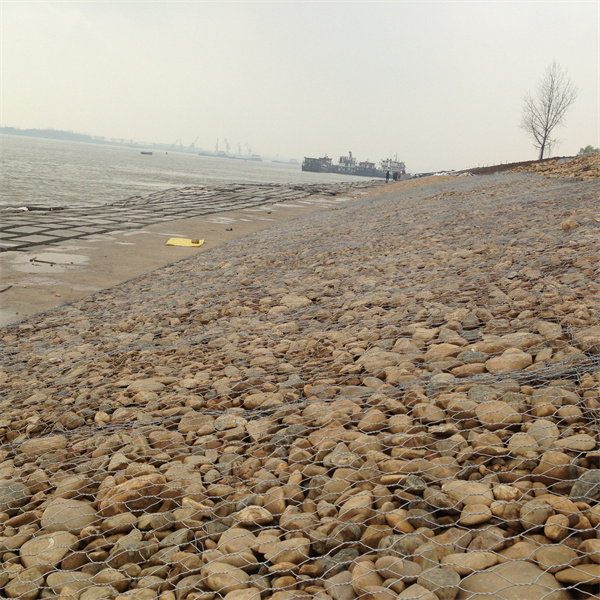
A critical aspect of gabion production is sourcing the right materials. Production lines equipped with state-of-the-art technology ensure that the wire used is of supreme quality, often galvanized or coated with PVC for enhanced durability. This treatment not only extends the life of the gabions in harsh environmental conditions but also provides an aesthetic edge, crucial for projects where visual impact is as important as functionality.
Mastery in production technology is essential for optimizing the various stages involved in gabion manufacturing. Precision machinery and automation play a pivotal role here. Automated systems facilitate meticulous wire cutting, bending, and welding processes, maintaining consistent mesh size and strength. This degree of precision is vital, as even minor discrepancies can compromise the structural integrity and longevity of gabion installations.
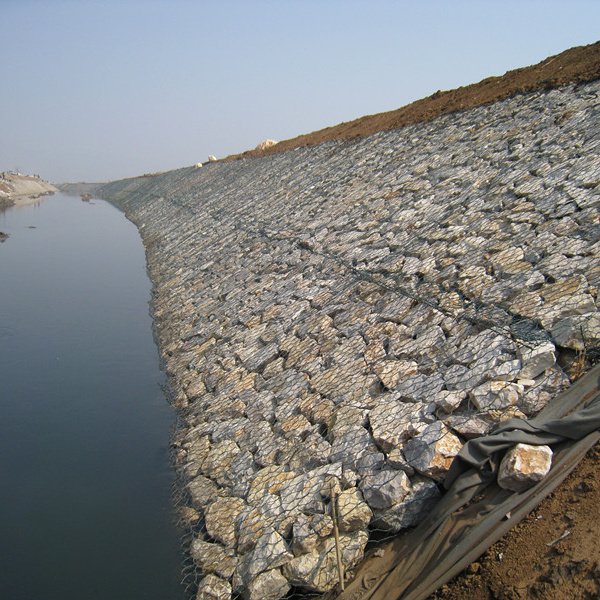
Moreover, leading production lines integrate cutting-edge technology that allows for customization according to client specifications. Whether adjusting the size of the wire mesh or experimenting with different types of infill materials, flexibility is paramount. Clients across sectors such as civil engineering, architecture, and landscape design benefit immensely from the capacity to tailor these units to the unique demands of their projects.
gabion production line
An often-overlooked aspect of gabion production lines is the attention to workforce expertise. Operators are trained extensively to handle advanced manufacturing equipment, ensuring that production meets both international and local standards. By combining human expertise with technological advancements, manufacturers can consistently produce gabions that are not only structurally sound but also aesthetically pleasing and environmentally sustainable.
Furthermore, stringent quality control mechanisms are employed throughout the production process. Each step, from wire selection to the final assembly, undergoes rigorous checks to guarantee that every gabion performs as expected in the field. This unwavering commitment to quality consolidates the trustworthiness of manufacturers in the eyes of their clientele.
In the context of sustainability, modern gabion production lines are increasingly adopting eco-friendly practices. The inclusion of recyclable materials and energy-efficient manufacturing processes minimizes the environmental impact, aligning the production of gabions with global sustainability goals. This is an attractive proposition for clients who prioritize environmental considerations in their projects.
In conclusion, the evolution of gabion production lines epitomizes a blend of technological innovation, skilled labor, and sustainable practices. As industries continue to demand high-quality, customizable gabion solutions, those manufacturers who prioritize technological advancement and stringent quality assurance continue to lead the field. Such dedication not only ensures the delivery of superior products but fortifies the reputation of gabion production as a reliable, durable, and environmentally conscious solution for today's ever-challenging construction and landscaping needs.